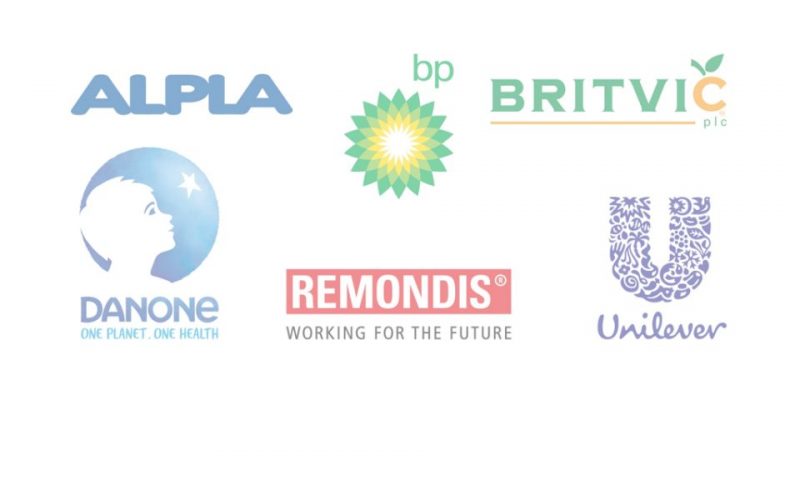
Leading Companies Join BP Infinia Enhanced Recycling Technology
Leading companies operating across the polyester packaging value chain – including businesses involved in the manufacture, use, collection and recycling of polyethylene terephthalate (PET) plastic packaging – today announced they have formed a new consortium that aims to help to address the problem of plastic waste by accelerating the commercialisation of BP Infinia enhanced recycling technology.
BP Infinia is designed to turn opaque and difficult-to-recycle (known as ODR) PET plastic waste, that can degrade in quality each time it is recycled using conventional methods, into recycled feedstocks that can be used to make new high-quality PET plastic packaging again and again, with no loss in quality.
The consortium intends to combine the capabilities and experience of its members – packaging and recycling specialist ALPLA; food, drink and consumer goods producers Britvic, Danone and Unilever; waste management and recycling specialist REMONDIS; and energy and petrochemicals producer BP – to develop a new circular approach to dealing with PET plastic waste.
PET is a plastic widely used for rigid food packaging and drinks, personal care and homecare bottles. It is a lightweight, durable and versatile material and one of the most collected and recycled types of plastic. Of the PET plastic bottles collected globally, more than 75 per cent are recycled, but only 12 per cent of those collected make it back into new bottles. The remainder is currently lost from the bottle-to-bottle loop 3, as it is used for other applications which are usually disposed of directly after use to landfills or incinerators due to lack of separate collection.
The consortium members believe by joining forces they can speed up the commercialisation of the technology, infrastructure and demand needed to process billions of opaque and difficult-to-recycle PET bottles and food trays that are currently disposed of each year, including those that are difficult to recycle by current conventional recycling methods.
It is the intention that each member of the consortium will contribute resources and distinctive capabilities and experience in areas such as waste management and recycling, technology development, intermediate processing and product design to develop a business model that takes into consideration the infrastructure, supply chain and demand requirements of all parties that will be involved in creating a circular economy for polyester and PET plastic.
In October 2019, BP announced plans to construct a $25 million pilot plant in the US to prove the technology on a continuous basis before progressing to full-scale commercialization.
Other parties may join the consortium in the future to complement the expertise of the founding members.
Quotes:
Georg Lässer, Head of Recycling at ALPLA:
“ALPLA is delighted to join this cross-functional project with partners from the entire value chain. It completes our intense activities besides mechanical recycling and focuses on post-industrial PET waste, difficult to recycle PET packaging and PET thermoform trays. With BP in the lead, we have a very strong and highly experienced partner that contributes with knowledge about virgin polyester production.”
Rita Griffin, BP Chief Operating Officer, Petrochemicals:
“This is an exciting step towards a circular economy for the polyester industry. BP is experienced in developing and scaling up technology and we’ll do this again with our innovative BP Infinia process. But we know we cannot create circularity on our own. That’s why we are thrilled to be working together with industry leaders to develop and prove a practical business model that can hopefully contribute to making all types of polyester waste infinitely recyclable.”
Trystan Farnworth, Director of Sustainability at Britvic:
“To truly reinvent Britvic’s packaging, we must innovate with new low-impact packaging. This consortium is a cornerstone to delivering that pledge. A challenge in creating a truly circular economy for PET is the fact that, as it stands, it is not infinitely recyclable. We have to solve this to become truly circular – it is not an option. That’s why we are excited to announce our active role in the consortium, collaborating to achieve a circularity breakthrough for the benefit of all our stakeholders.”
Katharina Stenholm, Danone’s SVP, Chief Cycles & Procurement Officer:
“Packaging is essential to ensure food safety and to reduce food waste, but it presents an environmental challenge. At Danone we commit to ensuring that our packaging will be 100% recyclable, reusable or compostable by 2025 and that our water and other beverages bottles will contain 50% rPET by then. We keep joining forces with partners and pooling expertise in order to develop innovative recycling solutions, create a second life for all plastics and thus accelerate the global transition towards a circular economy of packaging.”
Ralf Mandelatz, Managing Director of REMONDIS Recycling GmbH & Co.KG:
“In order to implement material circularity in PET packaging, we need new technologies for packaging that can’t yet be mechanically processed. We want this material resource to return into the circular economy; chemical recycling complements mechanical recycling and provides further possibilities to sustainable resource management. REMONDIS intends to contribute its specialist experience in the field of sorting and PET processing to the other consortium partners leading this European project.”
Marc Engel, Unilever’s Chief Supply Chain Officer:
“We’ve recently committed to halve our use of virgin plastic, reducing our absolute use of plastic packaging by more than 100,000 tonnes and accelerating the use of recycled plastic. We’ve also committed to help collect and process more plastic packaging than we sell by 2025. Joining this consortium is an investment in the future of recycling technology which is critical to keeping plastic in the loop. By working together, we can help accelerate the industry towards a circular economy.”